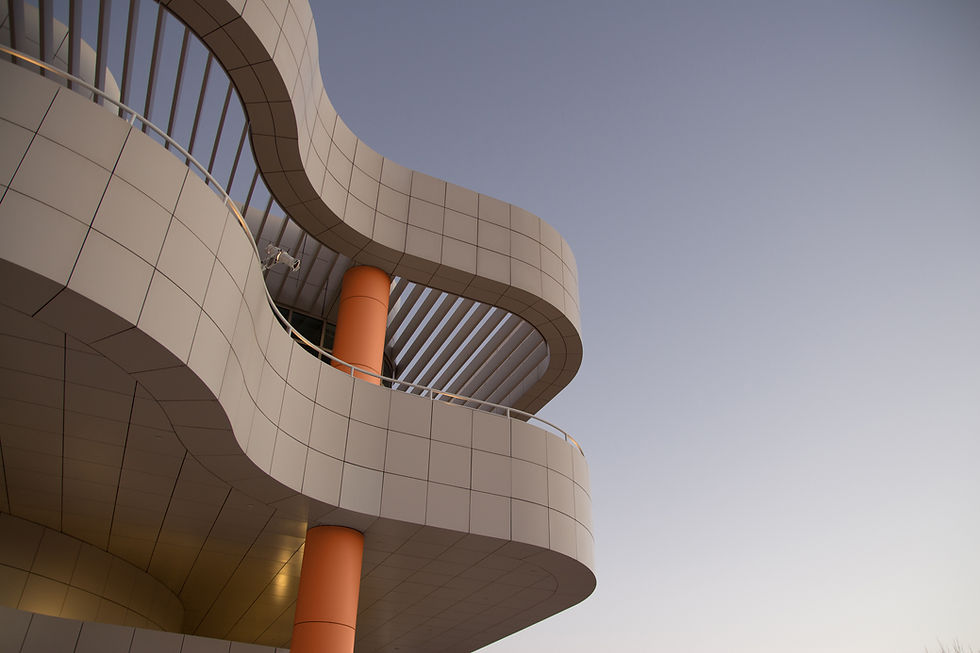
How to Highlight Lean Six Sigma Expertise in Genpact Interviews: A Guide to Showcasing Process Improvement Skills
Oct 14, 2024
5 min read
0
0
0
Genpact, a global leader in business transformation, places a strong emphasis on operational efficiency and process excellence. Lean Six Sigma is one of the core methodologies used at Genpact to help clients achieve these goals. If you’re preparing for a Genpact interview, demonstrating your Lean Six Sigma expertise can set you apart from other candidates, especially for roles focused on process improvement, operations management, or consulting.
In this blog, we’ll explore how to effectively present your Lean Six Sigma skills in a Genpact interview and explain the company’s focus on process improvement, particularly when preparing about Genpact company for interview.
Genpact's Approach to Process Excellence and Lean Six Sigma
Genpact’s origins as a business process outsourcing (BPO) arm of General Electric (GE) have shaped its focus on operational excellence and efficiency. Today, the company offers a wide range of services that include digital transformation, data analytics, and automation, making it a crucial partner for many Fortune 500 companies.
Lean Six Sigma is integral to the company's approach to process improvement. By combining the waste reduction principles of Lean with the defect reduction focus of Six Sigma, Lean Six Sigma provides a structured method for enhancing both productivity and quality. This makes it a key skill in various roles at Genpact, as the company constantly seeks ways to streamline operations and deliver better business outcomes for its clients.
Common Lean Six Sigma Questions in Genpact Interviews
To prepare effectively for a Genpact interview, especially for positions that emphasize process improvement, you need to anticipate questions about your Lean Six Sigma experience. Below are common Lean Six Sigma-related questions that may come up and how to answer them.
1. What is Lean Six Sigma, and how have you applied it?
This is a foundational question to evaluate your understanding of Lean Six Sigma and your ability to explain it clearly.
Sample Response:"Lean Six Sigma is a combination of two methodologies: Lean, which aims to reduce waste in processes, and Six Sigma, which focuses on reducing defects and improving quality. Together, they create a powerful framework for process improvement. I applied Lean Six Sigma in my previous role to streamline a procurement process, where we managed to reduce cycle time by 25% and cut costs by identifying and eliminating non-value-adding activities."
2. Can you provide an example of a process improvement project you led using Lean Six Sigma?
This question is designed to probe into your practical experience and how you can apply Lean Six Sigma principles to real-world problems.
Sample Response:"In my last role, I led a Lean Six Sigma project that focused on improving the order-to-delivery process for a logistics company. We started with a thorough data analysis to identify bottlenecks, which revealed delays in the communication between different departments. By implementing Lean techniques to streamline workflows and Six Sigma tools to reduce errors, we cut the process time by 30% and improved delivery accuracy by 20%."
3. How do you prioritize process improvement opportunities?
This question assesses your decision-making process when choosing which improvements to tackle first, a critical skill in a high-impact company like Genpact.
Sample Response:"I prioritize process improvement opportunities based on their potential impact on overall business performance, cost reduction, and alignment with organizational goals. I always start with a data-driven analysis, looking at where inefficiencies are costing the most time and money. For example, in a project involving supply chain optimization, we prioritized processes that had the highest defect rates, which led to significant cost savings."
4. How do you integrate Lean Six Sigma with digital transformation efforts at Genpact?
As Genpact is at the forefront of digital transformation, combining Lean Six Sigma with emerging technologies like automation and AI is crucial.
Sample Response:"I see Lean Six Sigma as a critical enabler of digital transformation. In a previous project, we used Lean Six Sigma to optimize a manual data-entry process, and then integrated Robotic Process Automation (RPA) to automate repetitive tasks, significantly increasing accuracy and reducing cycle times. Lean Six Sigma helped us first identify inefficiencies, and digital tools amplified the improvements."
5. How do you handle resistance to Lean Six Sigma changes within an organization?
Resistance to change is a common challenge in process improvement projects. Genpact values candidates who understand how to manage and mitigate this resistance effectively.
Sample Response:"Change management is key in any process improvement initiative. To handle resistance, I focus on communication and collaboration. I engage stakeholders early in the process and ensure they understand the benefits of Lean Six Sigma. In a recent project, we faced resistance from team members worried about job changes due to automation. By conducting training sessions and involving them in decision-making, we built trust and ensured a smooth transition."
Highlighting Your Lean Six Sigma Skills in Genpact Interviews
To impress your interviewers at Genpact, it’s important to effectively communicate your Lean Six Sigma experience. Here are some ways to make your skills stand out.
1. Demonstrate Deep Knowledge of Lean Six Sigma Tools
Make sure you’re well-versed in Lean Six Sigma methodologies like DMAIC, 5S, Value Stream Mapping, and Root Cause Analysis. The more fluently you can explain how these tools helped solve specific problems in your previous roles, the better you’ll align with Genpact’s process improvement culture.
2. Show Quantifiable Results
Lean Six Sigma is about driving measurable improvements, so use concrete data to back up your claims. If you reduced costs by 10% or improved process speed by 20%, make sure those figures are front and center in your answers.
3. Tailor Your Responses to Genpact’s Focus Areas
When preparing about Genpact company for interview, familiarize yourself with the industries they serve, such as financial services, healthcare, and consumer goods. Tailor your examples to show how your Lean Six Sigma skills are relevant to these areas. For instance, if you worked in healthcare, highlight how you reduced patient wait times or improved service quality.
4. Integrate Digital Tools with Lean Six Sigma
Genpact’s focus on digital transformation means that they are particularly interested in how you can blend Lean Six Sigma with emerging technologies. If you have experience using data analytics, AI, or automation to drive process improvements, make sure you highlight that.
5. Be Ready for Scenario-Based Questions
Genpact interviews often include scenario-based questions where you’ll be asked to solve a hypothetical business problem. Be ready to walk through your problem-solving process using Lean Six Sigma tools and methodologies.
Conclusion
Lean Six Sigma is a core competency at Genpact, and showcasing your expertise in process improvement can significantly enhance your chances of landing a job. By understanding about Genpact company for interview, highlighting quantifiable achievements, integrating digital transformation concepts, and emphasizing your ability to manage change, you can demonstrate that you’re the ideal candidate for roles requiring operational excellence.
Preparing thoroughly for Lean Six Sigma questions and emphasizing your experience with real-world examples will allow you to stand out during your Genpact interview.